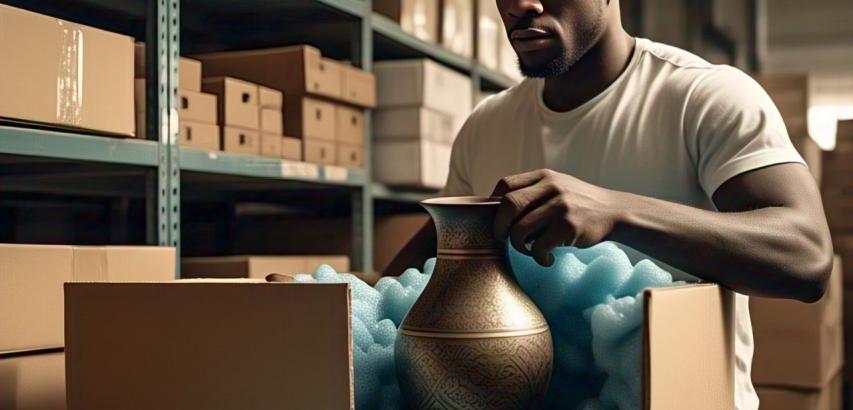
Expanding packaging foam is a versatile, lightweight material designed to secure fragile or irregularly shaped items during transit. Made from polyurethane or similar polymers, this foam expands upon application, conforming precisely to the shape of the product it protects. Widely used in e-commerce, manufacturing, and logistics, it offers a modern alternative to traditional packaging materials like bubble wrap, peanuts, or cardboard inserts.
Key Features and Technology
Expansion Process:
Dispensed as a liquid from an aerosol can or mixing nozzle, the foam reacts with moisture in the air to expand up to 30–40 times its original volume.
Sets into a semi-rigid, yet flexible structure within minutes, creating a custom-molded cushion.
Dual-Component Systems:
Some industrial-grade foams require mixing two chemicals (polyol and isocyanate) to trigger expansion, allowing precise control over curing time and density.
Customizable Density:
Available in low-, medium-, or high-density formulations to balance cushioning and weight.
Lightweight and Space-Efficient:
Reduces shipping costs by minimizing package weight and volume compared to bulkier materials.
Water and Dust Resistance:
Closed-cell foam structures repel moisture and contaminants, ideal for sensitive electronics or medical equipment.
Applications
E-commerce: Protects delicate items like glassware, ceramics, or electronics during delivery.
Automotive: Secures precision parts (e.g., sensors, circuit boards) in transit.
Art and Antiques: Custom-molds around fragile sculptures or frames.
Industrial Machinery: Fills voids in crates to prevent shifting.
Temperature-Sensitive Goods: Insulated variants maintain thermal stability for pharmaceuticals or perishables.
Advantages
Perfect Fit: Expands to fill empty spaces, eliminating movement and reducing damage risk.
Shock Absorption: Absorbs impacts and vibrations better than static materials like Styrofoam.
Reduced Material Waste: Requires less storage space pre-expansion and generates minimal waste post-use.
Sustainability Options: Bio-based or recyclable foams are emerging to address environmental concerns.
Cost-Effective: Lowers shipping expenses and insurance claims due to superior protection.
Considerations
Curing Time: Requires 1–5 minutes to fully expand and set, which may slow packing workflows.
Temperature Sensitivity: Performance can vary in extreme cold or humidity.
Chemical Handling: Uncured foam may emit volatile organic compounds (VOCs)—proper ventilation and PPE are essential.
Disposal Challenges: Traditional polyurethane foam is not biodegradable, though eco-friendly alternatives are gaining traction.
Over-Expansion Risk: Incorrect application can deform packaging or damage products.
Popular Products
Instapak® Quick RT: A fast-curing, single-component foam by Sealed Air for on-demand protection.
FoamPak®: Two-component systems for heavy-duty industrial use.
BioFoam®: Plant-based, biodegradable foam for eco-conscious brands.
Expanding packaging foam is a game-changer for industries prioritizing efficiency, cost savings, and product safety. Its ability to create custom, form-fitting cushions on demand makes it indispensable for high-value or fragile shipments. While traditional foams raise environmental concerns, innovations in bio-based and recyclable formulas are paving the way for greener solutions. For businesses seeking to optimize their packaging processes—without compromising protection—this smart material offers a forward-thinking answer to modern shipping challenges.
![]() | ![]() | ![]() |